Explore offsite and modular construction methods with Adrian Mitchell, Offsite Construction Business Specialist at Simpson Strong-Tie. Learn how these methods can address housing shortages and help engineer a more efficient and sustainable future.
I was looking out over the skyline of downtown Vancouver recently and couldn’t help noticing that the great majority of the buildings looked almost identical in their architecture. And yet, as a modular and offsite construction specialist for the last ten years, I’ve heard from many potential developers and designers that modular and prefabricated systems ought to allow for more creativity and flexibility.
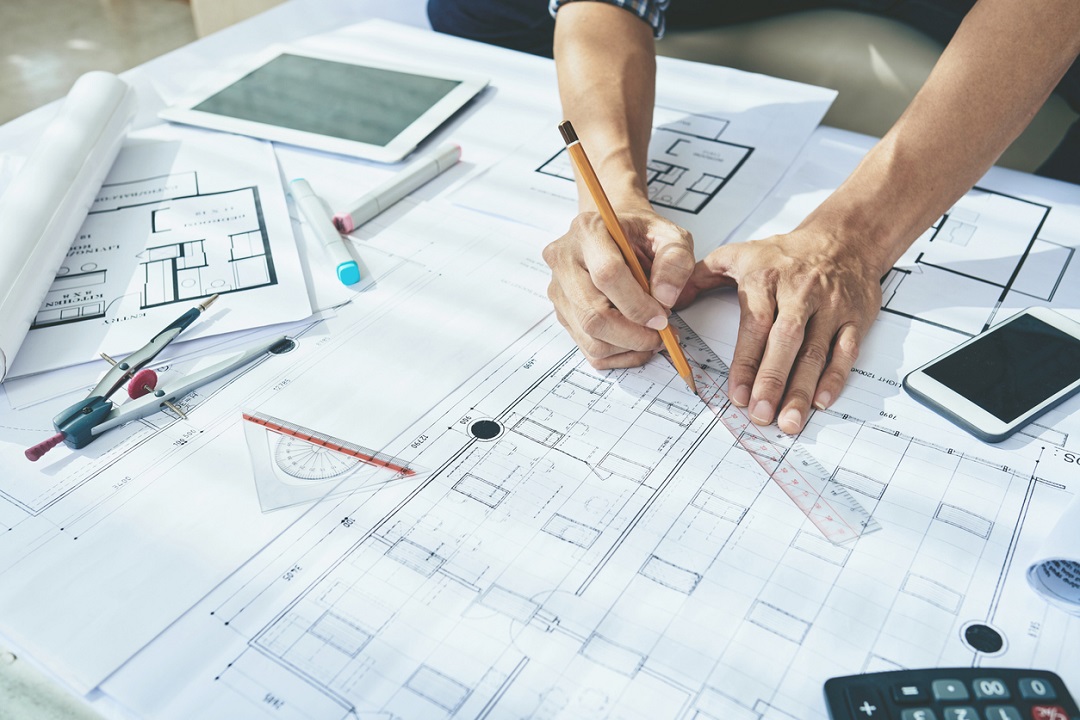
I empathize with how many variables architects must manage in designing a new project. Zoning, unit mix, height and view corridor limitations, natural light and articulation are all key considerations. And as important as all these factors are, developers and owners also require designs that are affordable. In the end, economic considerations frequently convert unique architectural concepts into generic skylines.
Given that a developer’s bottom line so often dictates project design outcomes, are there alternative approaches that designers can offer that stand a reasonable likelihood of meeting the developer’s needs? How can architects and engineers take advantage of the opportunities presented by offsite and modular construction to create better outcomes for their clients and a more stable demand for their services?
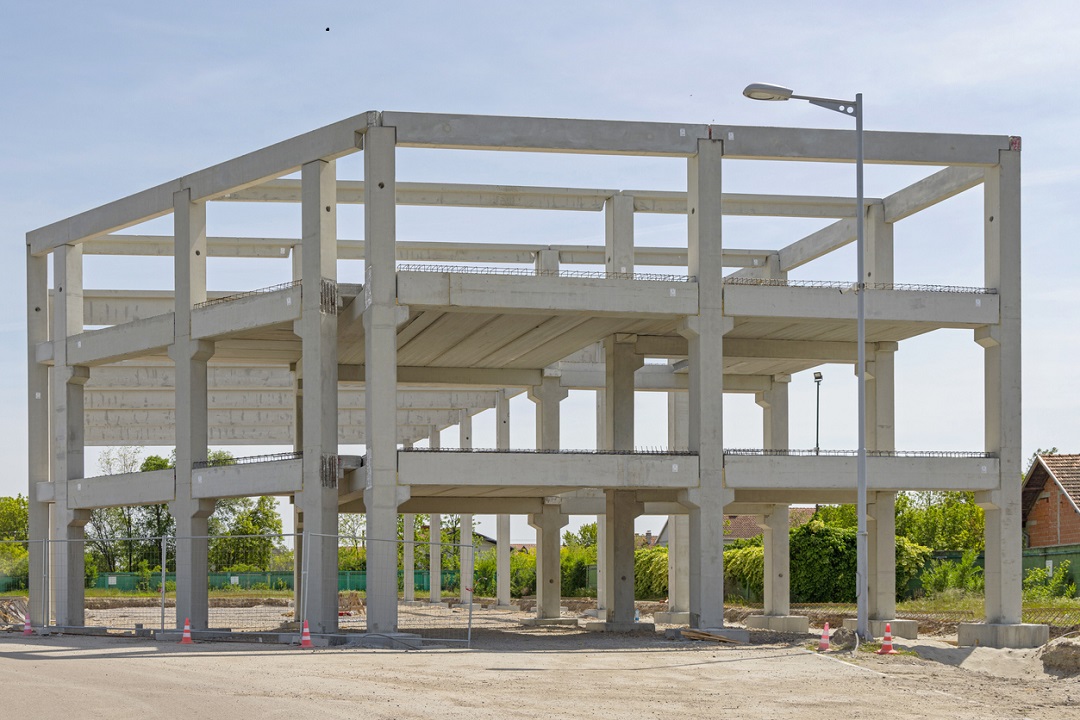
Offsite and modular building methods offer the advantage of incremental improvement. Utilizing a modular parts kit, we can create much larger supply chains and gradually refine building system details over time, creating substantial quality increases and cost reductions with every new building. An excellent offsite system will allow for design flexibility without sacrificing the economies of scale and efficient material supply chains needed to keep costs low.
What does an offsite system look like? How can design professionals get started in this space? The answer doesn’t lie in adopting complex and detailed building systems that might take years to develop. The answer lies in adopting standardization in smaller bites, with the goal of implementing a kit of parts for all aspects of a building design.
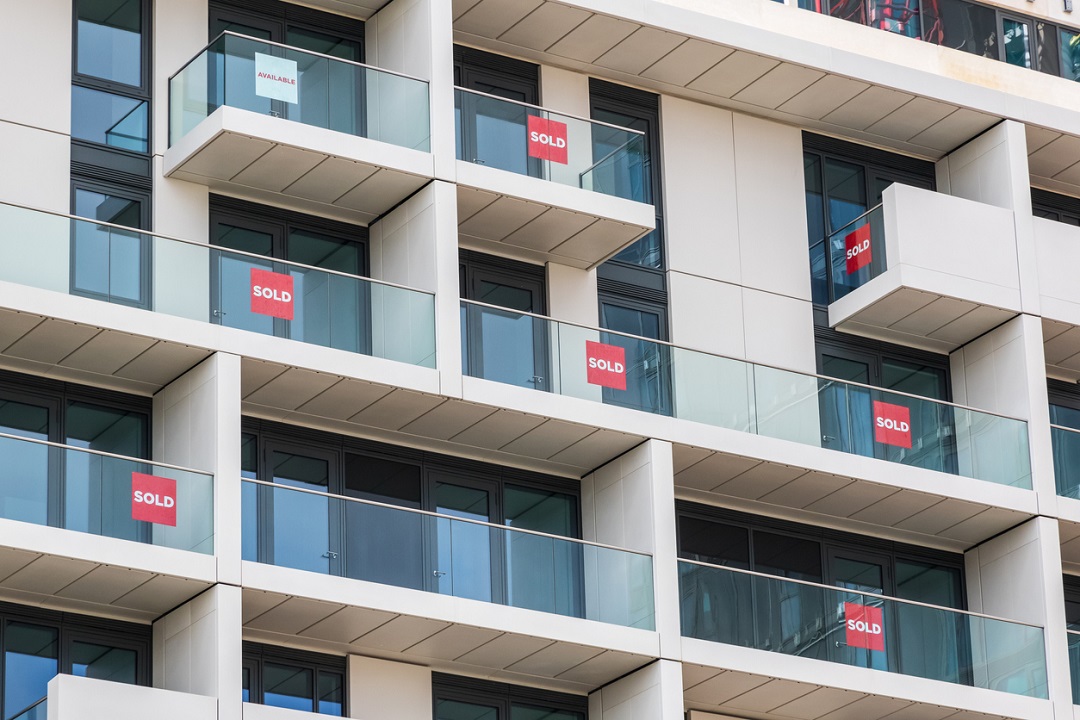
The current housing crisis facing many cities in North America offers us an ideal climate for product standardization. Our longstanding housing shortage ensures a durable demand for well-designed multifamily buildings. Starting with a scalable structural system is an ideal first “bite” for building designers.
Standardized or parametric grids can allow for the mass production of structural components using high-precision manufacturing, fostering higher precision on the jobsite as well. The incremental nature of such an approach also allows improvements at every stage following the principle of Kaizen, a Japanese expression that translates as continual improvement. In other words, the method encourages system optimizations over time, ensuring that we learn from mistakes and use those lessons to our advantage both as we progress with the project and as we take on future projects.
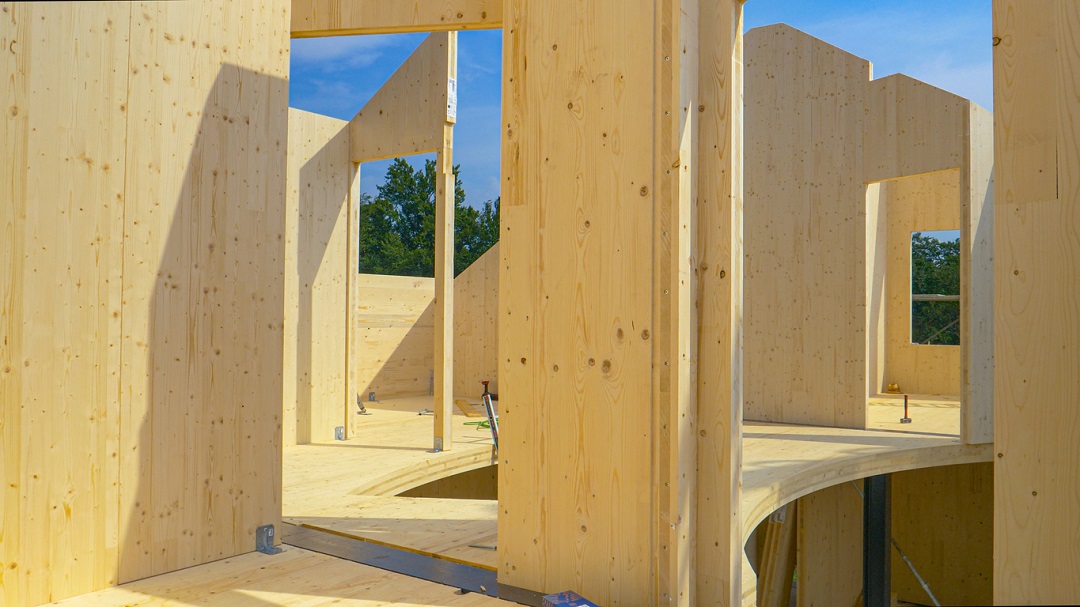
If economics require us to build our high-rise or mid-rise condos and office buildings in a uniform style, it makes even more sense to look into offsite, modular, and mass timber construction methods. Automation and manufacturing can address shortages in housing and in skilled construction labor. The time for industrialized construction is here, and the opportunity to build a career as an architect and developer is unprecedented!