Safety Banner inside a Simpson Strong-Tie warehouseIn the safety field, the Total Recordable Incident Rate (TRIR) is the best-known measure of the strength of a company’s occupational health and safety program. It’s calculated as a ratio of the total number of OSHA-reportable injuries per 100 full-time workers over a period of time. We have met our TRIR goal for 11 out of the last 12 months and continue to challenge ourselves to drive that number downward by working alongside other departments to build a comprehensive, sustainable safety program that truly has no equal.
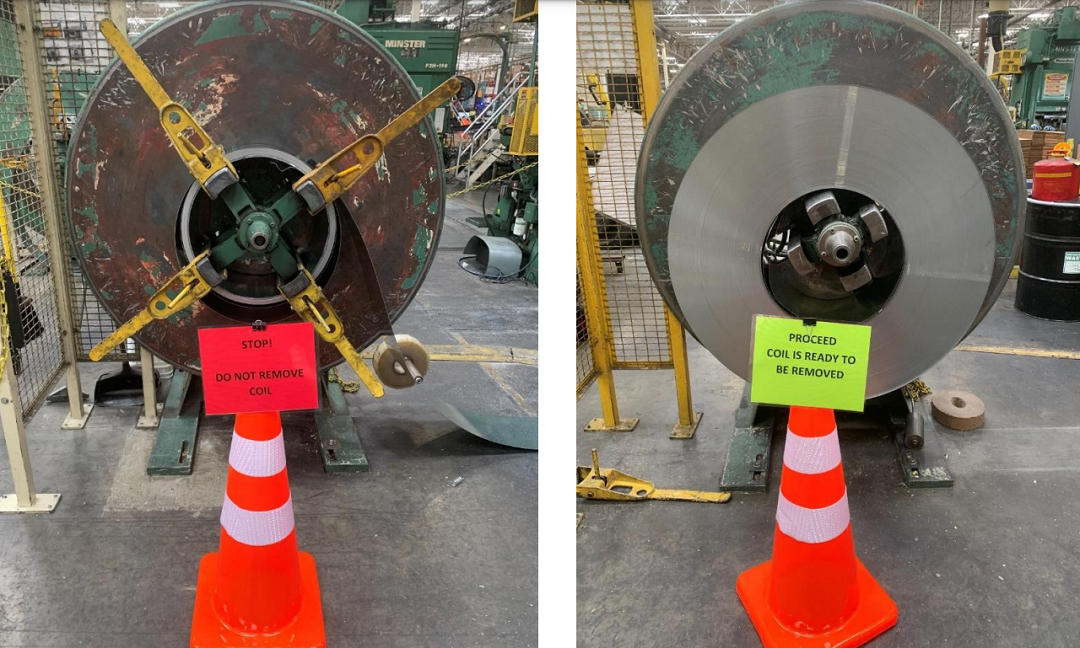
We do this by providing training, implementing policies and procedures that protect our people, teaching employees at all levels to identify potential safety hazards before they become a problem, and leading investigations of the incidents that do happen in an effort to prevent recurrence. The safety team at each branch is charged with creating and managing employee participation programs to get every employee involved in identifying and reporting safety hazards. As some of our banners around the plant say, “Safety is everyone’s business.”
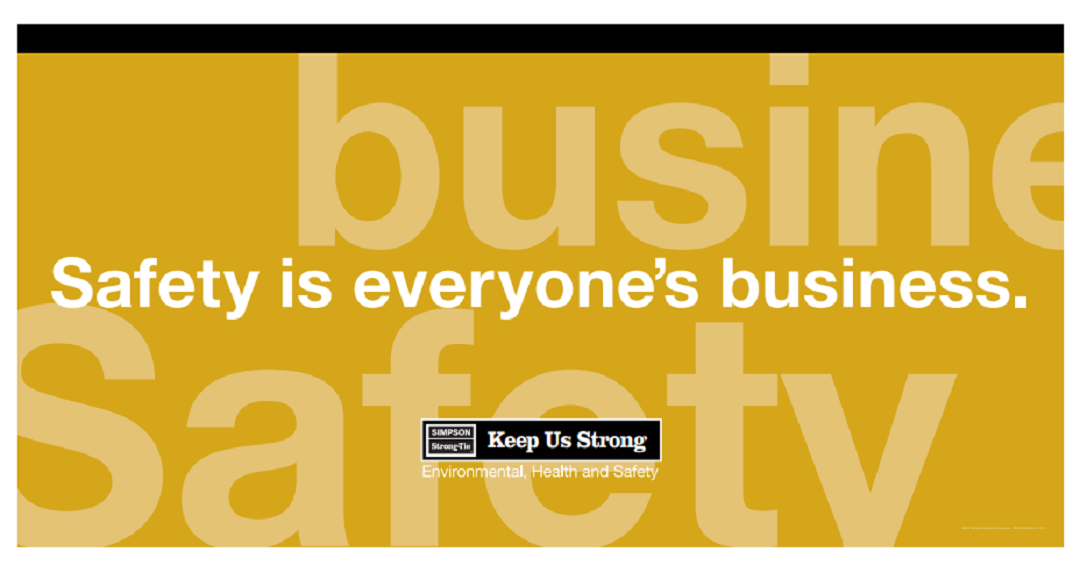
Our Global EHS team is a growing, dynamic group. In the past two years, we’ve added three full-time EHS coordinator positions and two EHS manager positions at our Columbus, Ohio; McKinney, Texas; and Gallatin, Tennessee branches, and expect to add more in pace with the growth of the company.
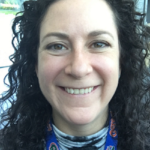
I am one of those EHS Coordinators, joining Simpson in April 2021 at the Columbus branch. With 12 years of safety experience at medical research institutions, I knew I would need to build on my knowledge of regulations that apply to manufacturing. Fortunately, the EHS Manager at Columbus, Tony Powers, has 25 years of experience starting on the shop floor and then becoming a full-time safety professional. The management team in Columbus was very welcoming, and when I learned that they give us up to an hour each month to train the shop staff, I saw how supportive they would be.
The North American EHS team, which meets weekly, also welcomed me with open arms and continues to be an indispensable resource. We share best practices and recommendations from our individual branches on how to tackle safety issues, both in and out of our weekly meeting, which makes all of our jobs easier as well as more fun. In addition, we have also recently added a second-shift EHS Coordinator in Columbus, John Chester, who is already proving himself to be a huge benefit to our program.
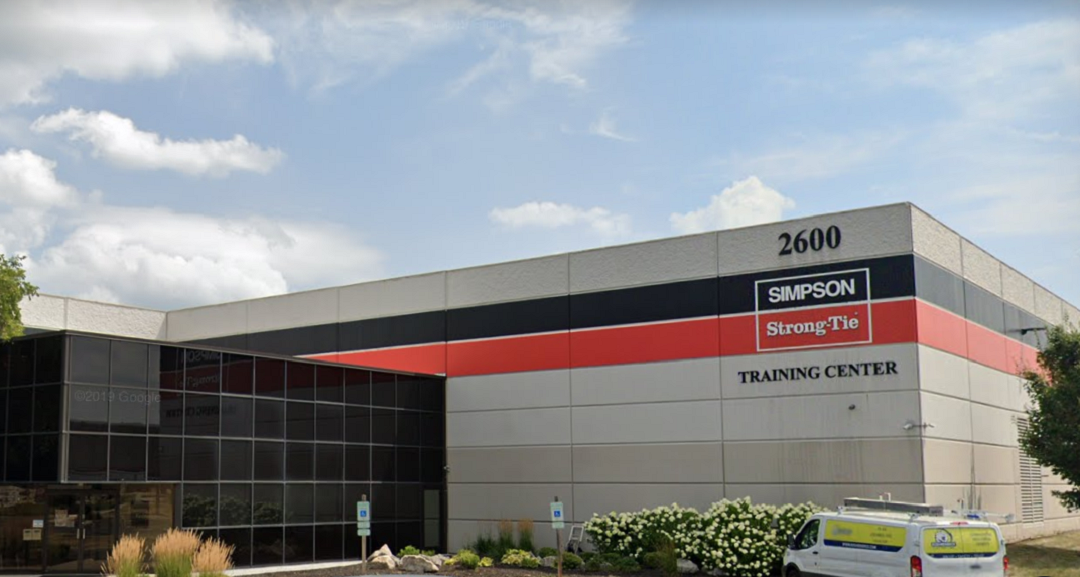
One of the highlights of my time at the Columbus branch so far was when Mike Olosky, President and COO, visited our branch in May 2021. We were about to begin a large meeting to welcome Mike and introduce him to our operations. I had never met Mike, but when he entered the warehouse floor from the office area, he somehow knew I was involved with safety and stopped to ask whether it was okay to bring his cup of coffee onto the shop floor. Seeing that the paper cup had no lid on it, I offered to get him one and was told that, unfortunately, we had run out.
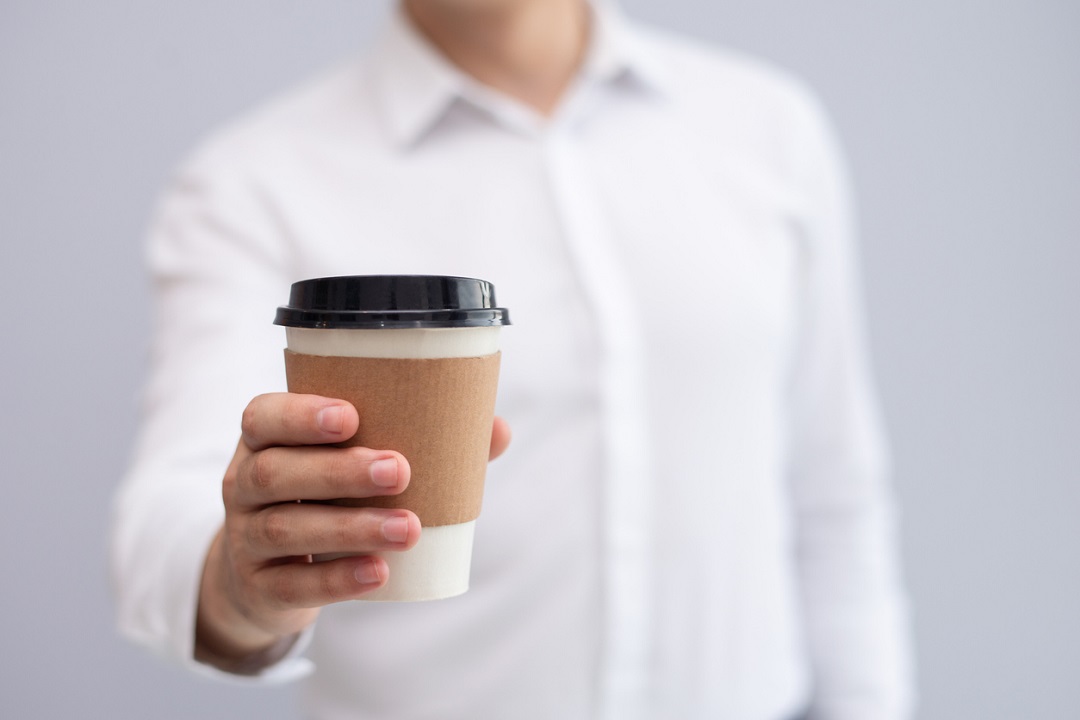
Only closed beverage containers are allowed on the shop floor, but I was going to give him a one-time pass. I mean, this is the President and COO of the entire company! I had been with Simpson for only a month, and the meeting was just barely outside the office door, with minimal risk of contaminating his beverage or causing any other safety hazard. I could tell he didn’t want to break any rules, but also really wanted the coffee— which, as a coffee drinker, I understand completely. When I told him it would be okay “just this once,” he immediately declined and went back into the office area to put his cup down before rejoining us for the meeting.
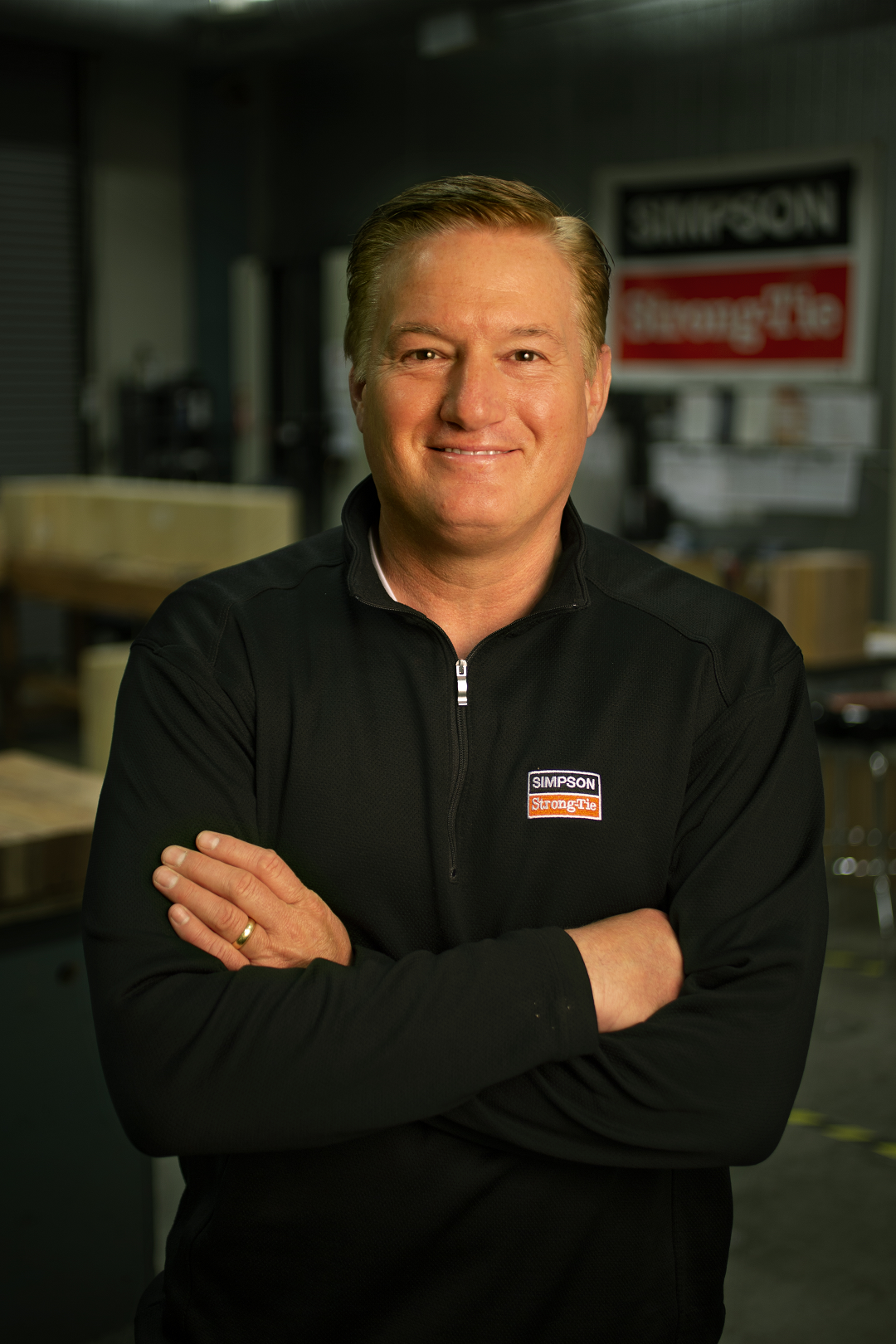
It may seem like a small thing to some, but to say I was impressed would be an understatement. I thanked him and smiled. Mike then went one step further and took the opportunity to lead the meeting with safety, by stating how we all need to put safety first and follow the same rules to support our safety culture, no matter who we are in the organization. I was floored! Trying not to show my pleasure too outwardly, on the inside I did a happy dance and threw confetti in the air.
That one simple act solidified for me that at Simpson Strong-Tie, we really do mean it when we say, “safety first.” I’m proud and honored to be a part of this team, and excited to see what we will accomplish together in the years to come.