Modular construction — sometimes also known as prefabricated, prefab, prebuilt, manufactured, factory-built, or panelized construction — ain’t no stroll in the trailer park. Although double-wides and modular prefabs sometimes roll off the same factory floor, the similarities end there between mobile homes and true modular construction, which is gaining a foothold in markets as builders and developers look for higher-quality, more efficient construction processes.
Like component construction, modular building takes much of the labor off of the construction site and puts it on a factory floor, where assembly can be value-engineered to minimize waste and maximize speed and overall product quality. And while modular building includes trusses and panels, modular component facilities are much more than your run-of-the-mill truss plant.
“There’s a saying in the modular industry: the only thing you have to do is put the log in the fireplace,” explains Erin Barker, territory manager for Simpson Strong-Tie. “Everything is assembled and included down to the electrical and the carpet. The builder buys from the modular plant, assembles the modular boxes onsite, and sells the finished building to the end user.”
Unlike stick-built structures, modular buildings require specialized set crews to connect modular units at the jobsite. But despite the need for skilled labor, modular buildings come together remarkably quickly, assembling into a completed structure in days instead of weeks or months. In 2015, a Chinese modular builder completed a 57-story skyscraper in just 19 days, and here in the US builders like Philadelphia-based Vaughan Buckley can finish an 18-unit apartment building in about a week.
While modular building has its roots in single-family residential construction (and still thrives with that segment), modular plants in Barker’s eastern Pennsylvania and southern New Jersey markets are increasingly providing low- and mid-rise multifamily product for apartments and student housing, primarily constructing modular units from wood or (less commonly) cold-formed steel. Each plant is required to have a third-party inspector, which can add to the overall quality-control advantages of precision-built construction over site-built framing.
“Don’t forget the boxes are also built to withstand driving down the freeway at 55 miles an hour to the jobsite,” says Barker, who adds that modular plants rely heavily on connectors like the new MMHC hinged roof connector, MMLU series of joist hangers and Quik Drive® collated drywall screws for tight, stable fabrication. “So we’re talking about extremely soundly built product.”
Modular construction isn’t without its challenges, though. Perception of the product as mobilehome-esque persists, and getting completed units delivered in small, dense or urban neighborhoods can involve complex logistics. “There are some limitations,” says Barker, who helps modular builders value-engineer construction processes to minimize costs or find more efficient connector arrays. “There may be some custom, high-end designs that are not yet attainable in modular, but in no way are we talking about trailer-park construction anymore. That is a different product altogether. Sometimes the same factory, but altogether a different product.”
In sum, the advantages of modular construction are making themselves better known throughout the building industry, and we can expect to see more and more panel-built homes, offices and other modular structures in the years and decades to come.
Build It Faster. Build It Better.
Speed, Strength and Versatility
In the modular construction industry, quality and efficiency matter most.
That’s why we’ve tailored our product line to offer innovative solutions that save time in manufacturing and on the jobsite—while providing the strength, flexibility and reliability you depend on.
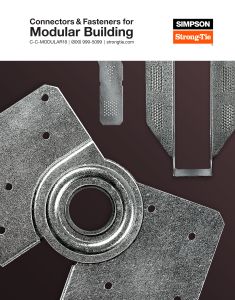